Table of Contents
Silica Dust: The Risks and Our Controls
What is Silica?
Silica dust is a fine, airborne powder that is released during activities like grinding, cutting, or polishing various materials. It is most commonly found in substances such as marble, granite, quartz, sandstone, pottery, and cement.
One material that has gained attention due to its high silica content is quartz, particularly in the production of quartz worktops. These work surfaces can contain as much as 95% silica. If not properly processed, handled, or cut, quartz surfaces can release harmful silica dust. It’s important to note that quartz surfaces themselves are safe for end users in normal applications; they become a health hazard only when they are cut or manipulated, releasing silica dust into the air.
Short-term exposure to silica dust does not typically cause damage, but long-term, repeated exposure can result in Silicosis, a serious and incurable lung condition. This can develop over a period of five years or more of continuous exposure to silica dust.
How Are We Controlling the Risks?
As a responsible employer, the safety and well-being of our employees are paramount. We have implemented several controls and safeguards to mitigate the risks of silica dust exposure:
1. Water-fed Bridge Saws
Our bridge saws are equipped with a water feed system that sprays copious amounts of water onto the cutting blade, keeping the dust particles from becoming airborne. This significantly reduces the risk of inhaling silica dust.
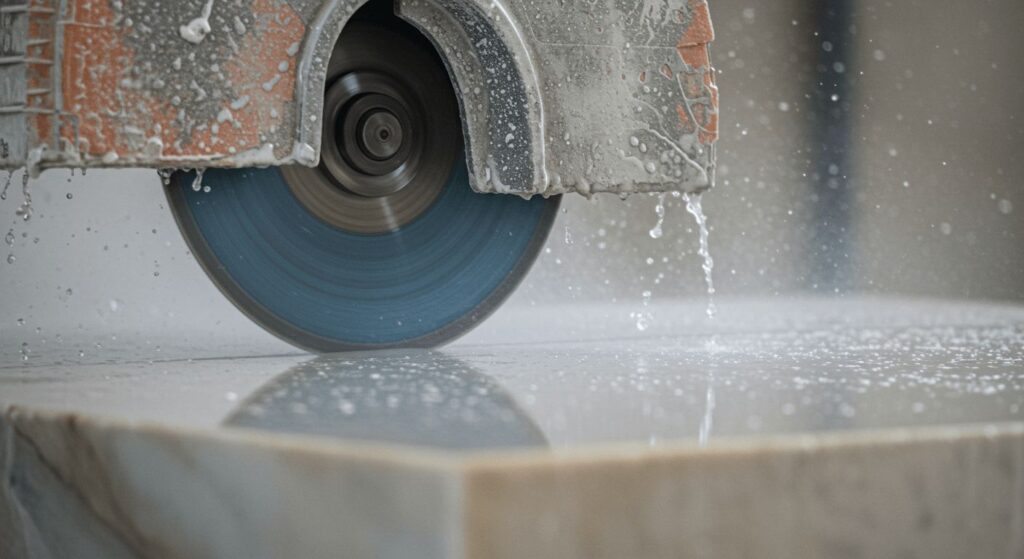
2. Wet Booths for Hand Cutting
Any cutting done manually is performed in water-extracted wet booths, further minimising airborne silica dust.
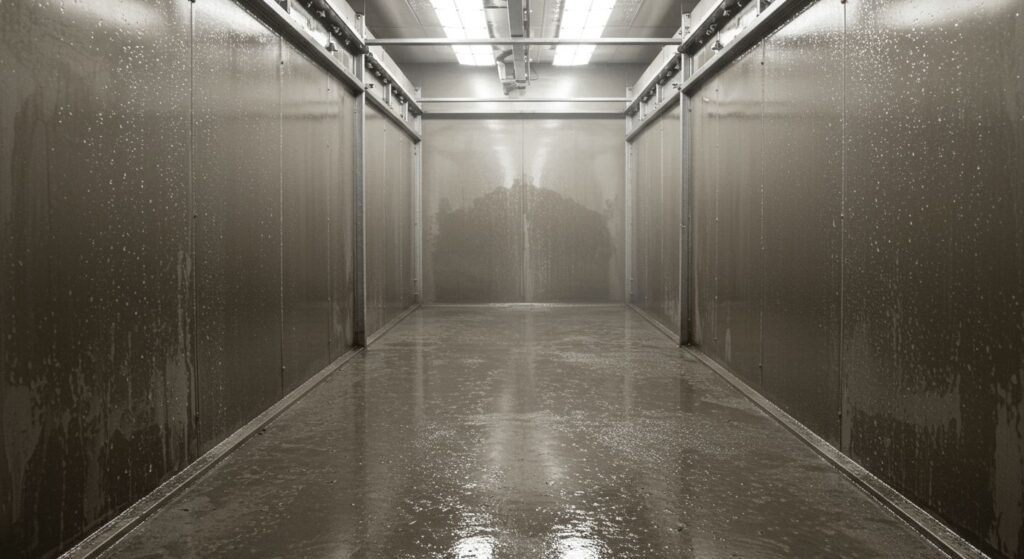
3. Water-fed Handheld Polishing Equipment
Our hand-held polishing tools also use water to ensure that dust is kept under control while polishing surfaces.

4. Protective Equipment
Our fabrication team is outfitted with the latest technology air-fed hoods and protective suits to provide extra protection against inhaling harmful dust particles.
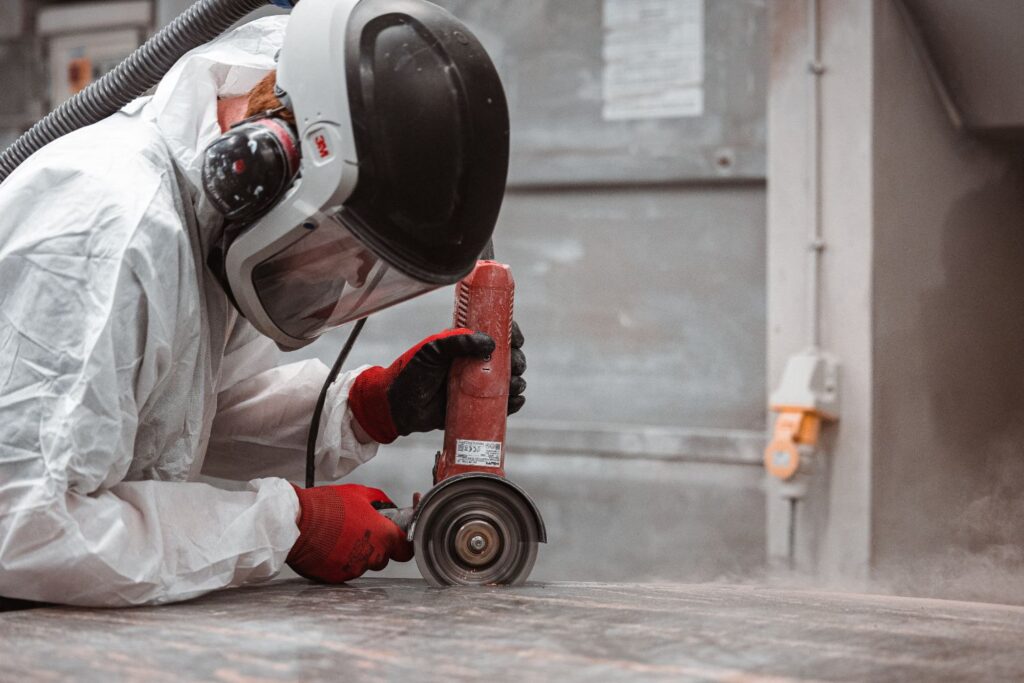
5. Regular Health and Safety Audits
We received recent visits from the Health and Safety Executive (HSE) and more frequent scheduled safety audits by our consultants at Opus Safety. These audits ensure that we comply with the latest safety legislation and industry best practices.
6. Commitment to Employee Welfare
We are dedicated to ensuring the safety of our workforce. Along with taking the necessary precautions to safeguard their health.
7. Responsible Employers
We ensure that our employees receive fair remuneration packages that reflect their skills and dedication.
Our Approach to Safety and Value
We understand that safety measures like the ones we have implemented come at a cost. With the investment detailed above, we are on occasion unable to compete with some other fabrication companies and associated quotations on the market.
From decades of trading, we have received feedback that our clients take reassurance that, whilst we are not and do not aim to be the cheapest on the market, we offer an expertly produced product at a value that ensures the safety and welfare of everyone involved in its production.